当前位置:
天津 恒永兴金属材料销售
有限公司 >孝感当地综合推荐News
铝合金型材【石油裂化管】一站式厂家
更新时间:2025-02-20 00:10:56 浏览次数:12 公司名称:天津 恒永兴金属材料销售 有限公司
以下是:铝合金型材【石油裂化管】一站式厂家的产品参数
产品参数 | |
---|---|
产品价格 | 335 |
发货期限 | 电议 |
供货总量 | 电议 |
运费说明 | 电议 |
品牌 | 恒永兴 |
规格 | 齐全 |
价格 | 电议 |
以下是:铝合金型材【石油裂化管】一站式厂家的图文视频
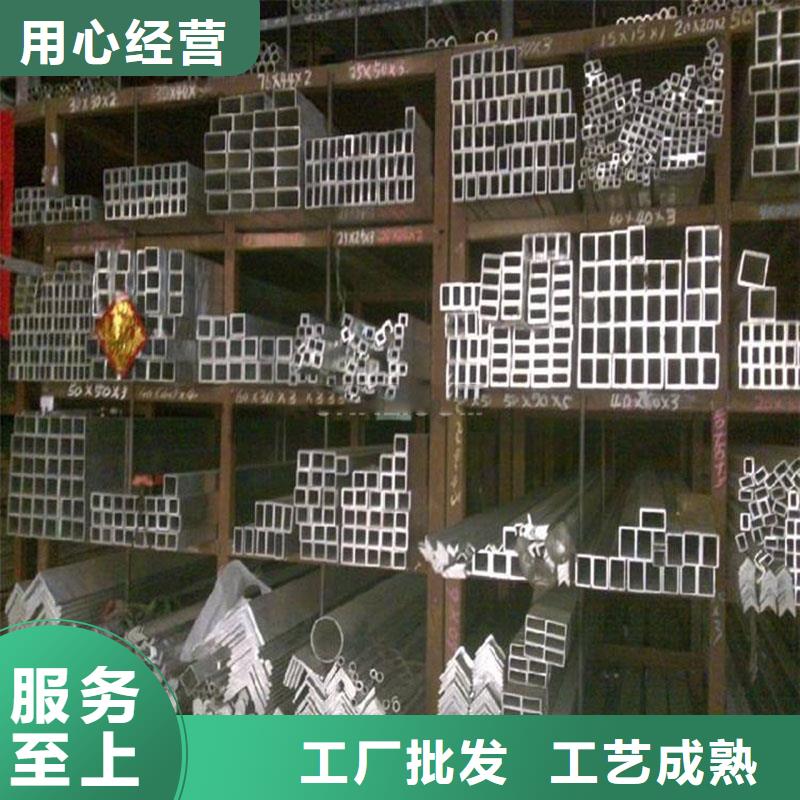

铝合金型材【石油裂化管】一站式_恒永兴金属材料销售
有限公司,固定:18802286588,移动:022-86869388,联系人:李经理,QQ:554918566,天津北辰区双街镇京津路西(北方实业发展有限公司内)到湖北省 孝感市 孝南区、孝昌县、大悟县、云梦县、应城市、安陆市、汉川市 到 湖北省孝感市。 湖北省,孝感市 孝感市,别称孝城,湖北省辖地级市,市境位于北纬30°23′—31°52′,东经113°19′—114°35',地处湖北省东北部、长江以北、汉江之东,与武汉市接壤,城区距离武汉市中心约60千米,距离武汉天河国际机场约30千米;地貌自南向北为平原、丘陵、山区,气候兼有南北之优;截至2023年,下辖1个市辖区、3个县、代管3个县级市,总面积8910平方千米;2022年末,孝感市常住人口418.58万人。
铝合金型材【石油裂化管】一站式的详细视频已经上传,从产品的外观到内在,从功能到性能,视频将为您呈现一个真实、全面的产品形象。
以下是:铝合金型材【石油裂化管】一站式的图文介绍
近年来,随着绿色建筑的推广,铝模板顺应趋势,在建筑领域发展强劲,逐步替代了木模板,迎来爆发;与此同时,其应用范围逐步扩大,从民用建筑向公共建筑延伸,地铁、隧道等工程也开始使用铝模板,国内各大型房地产商如保利、万科和碧桂园等均大规模应用,铝模板行业也逐步形成完善的施工体系。铝模板行业之所以在近年迎来爆发增长,主要得益于其在产品性能、技术应用和经济成本等方面的优势。NO. 1性能优势:铝模板自重比全钢的模板轻、装配与周转方便,结构成型的效果也很好。在欧美等 铝模板已成功的推广十多年,在我国的港澳地区铝模板也得到了广泛应用。铝合金模板在实际中的应用:游泳馆的馆顶遮阳棚,化工业等产业的厂房,体育场(鸟巢)。国外的丰田博物馆、康涅狄克大学及夏威夷大学的竞技场、贝尔竞技中心等都是铝合金模板在现实生活中的实际应用实例。NO.2技术应用优势:由于铝模板的自重轻,且模板承受压力的条件好,很方便混凝土机械化、快速施工的作业;以标准板加上局部非标准板的配置板,并在非标准板上采编号的技术,相同构件的标准板是可以混用的,这使拼装的速度更快;铝模板在拆装的时候操作也更加的简便,拆卸和安装的速度更快;模板与模板之间是用销钉进行固定,安装也方便多了。因为采用了早拆的设计,水平构件模板在36小时后便可拆除。模板在安装的时候设有便于移动的多级操作的平台,确保模板安装、拆卸时作业人员施工的安全;铝模板在拆除后混凝土表面质量是很好的。按照计划施工,可确保模板安装平整、牢固,确保混凝土的表面达到清水混凝土的效果。NO.3经济成本优势:铝模板不像木质模板那样只能使用一次就变形,相比之下铝制模板使用的次数多,全铝合金模板施工中使用的次数明显高于钢模板、木模板、组合大模板等,在层数高的超高层建筑施工中优势显著。经过核算,一套全铝合金模板只要使用的次数超过50次,成本即与传统的木模板摊销单价持平。另一个优点就是节约工期,减少大型设备租金与其他模板相比,铝模板具有方便、快捷等诸多优点。铝模板在本项目结构层施工过程中平均节约工期两天每层。应用铝模板的工程在面层免抹灰上,成本降低很大一部分,结构面的效果确可以达到清水混泥土的效果,到了装修的阶段,内墙面可以省去抹灰和平正的工序,从质量上直接杜绝了室内墙面抹灰空鼓和裂缝的通病。历经木、钢、竹、塑等模板材料的更新换代,铝模板作为全新第五代建筑模板材料,以其独特优势,成为模板行业的新宠。
在过去的几年合作中,恒永兴金属材料销售
有限公司由于 湖北孝感架子管供货及时,质量可靠,受到了各用户单位的一致好评。
未来我公司宗旨:以质量求生存,靠信誉求发展,诚信为本,创新为先,以质取胜。
铝合金型材的壁厚是重要的质量指标,建材标准与门窗标准分别对壁厚进行了规定,特别是门窗标准《铝合金门窗》GB/T8478规定了受力杆件的壁厚要求。本文主要从标准的规定、受力杆件的受力部位、壁厚的测量等方面进行了说明,介绍了铝型材壁厚相关内容。铝合金门窗因其强度高、表面处理颜色多样化、门窗性能优越等特点越来越受到大家的欢迎,铝合金门窗型材产品也成为大多铝材厂的主要产品。门窗铝型材生产时执行国标,并符合合同的相关要求,而型材壁厚是重要的质量指标, 相关标准也对型材的壁厚作出了规定。本文主要对门窗型材的壁厚谈谈个人的理解。一、标准对壁厚的规定:国标《铝合金建筑型材第1部分:基材》GB/T5237.1-2017是铝型材厂执行的标准。标准规定ABC三类壁厚的公差标准,通过标准可知,型材壁厚执行正负公差,并有精度等级之分。如门窗型材壁厚为1.4mm,外接圆小于100mm,按高精级,则A类壁厚公差是±0.13mm。国标《铝合金门窗》GB/T8478-2008是门窗加工的标准,其中对于铝型材的壁厚有明确规定,门不小于2.0mm、窗不小于1.4mm。上海地方标准《民用建筑处窗应用技术规程》DG/TJ08-2242-2017中规定铝型材壁厚不小于1.8mm。福建地方标准《福建省民用建筑外窗工程技术规范》DBJ 13-255-2016中规定铝型材壁厚不小于1.6mm。二、受力部位壁厚示意:在标准中虽然定义了门窗主要受力部位,但在实际应用过程中不是特别顺畅,有时也存在争议。对于受力部位,我个人的理解是型材的主要腔体一周、主要翅部、及安装五金的槽口等部位。其他部位比如胶条槽口、角片槽口等就不是主要受力部位。三、壁厚测量方法:铝型材壁厚使用千分尺测量,测量精度为0.01mm。不建议使用游标卡尺测量壁厚,因为使用游标卡尺测量时的力度不好掌握,测量结果会因人而异。而千分尺有棘轮设置,能够保证测量施加力度符合要求,多次测量结果一致。壁厚测量要注意精度问题。标准要求是≥1.4mm,精度为小数点后一位,那么测量壁厚的数值精度同样保留一位小数是否合适呢?例如,测量壁厚数值为1.35mm,保留小数点1位,按数字修约规则“四舍五入”及“四舍六入五留双”修约后记录为1.4mm,从数据上看是符合≥1.4mm的要求的。那测量结果为1.35mm壁厚的型材符合标准要求吗?个人理解为,标准规定壁厚≥1.4mm,目的是提高型材的质量,实际产品壁厚要厚些,且要达到1.4mm。所以测量结果为1.35mm壁厚的型材不符合标准要求。测量壁厚时,还要注意壁厚为测量面的任意点壁厚,如果测量面上有一处的壁厚不符合要求则产品不符合要求。壁厚指标不是测量的平均值,而是任意点壁厚。见图8,图中标记红色部位壁厚为1.35mm,即使平均壁厚达到1.4mm也不符合壁厚≥1.4mm的标准。总之,门窗标准对铝合金型材壁厚的规定提高了门窗整体性能,铝型材生产与门窗加工单位对此应加深理解,生产出符合国标的门窗。铝型材受力杆件壁厚的问题一直是门窗相关企业关心的问题,大家对于哪个部位是受力部位理解也不尽相同,我们要严谨对待标准的要求,从而提高产品质量,为铝合金门窗行业作出贡献。
铝型材散热器生产工艺:首先贴膜不能直接贴在铬化层上,否则会影响膜的附着力;其次,贴膜后要及时喷涂不能停放时间过长,否则容易导致贴膜脱落,严重时还要重新贴膜;再次是撕膜时要控制流平时间,不能贴膜后马上撕膜,这样会对产品质量带来一定的影响;*后是两种颜色的喷涂顺序要根据具体情况确定,既要考虑到两次固化,又要考虑到遮盖效果。贴膜质量控制:散热器铝型材质量控制中贴膜质量很重要,若贴不好,会导致喷涂困难,如贴膜的张力不大、压紧程度要控制好;对形状复杂的部位要分开贴膜,贴膜后要检查贴膜是否贴牢。否则将会给喷涂带来麻烦。影响喷涂质量。公司生产的铝型材产品均由专业的技术人员严格把关,并拥有专业的生产设备,保证质量问题,客户可放心选购我厂产品。铝型材散热器的贴膜材质:首先要对贴膜材质合理选择,根据散热器铝型材产品的要求、表面处理方式,选择相应的贴膜,同是还要考虑贴膜上的胶对铝型材表面质量的影响。
缩孔是铝合金压铸件常见的内部缺陷,常出现在产品壁厚较大或者易形成热点的位置。一般来讲,只要缩孔不影响产品的使用性能,都以合格的方式来判定。然而,对于一些重要部位,如汽车发动机汽缸体的冷却水道孔或润滑油道孔,出现缩孔是不允许判定合格的。
某企业的一款铝合金制发动机曲轴箱,采用布勒28000kN冷室压铸机铸造,材质为ADC12合金,成分见表1。铸件毛坯质量为6.3 kg,后工序进行X射线探伤时发现第二个曲轴轴承孔油道出现缩孔,离油道约8 mm,存在较大的漏油风险。据统计,2017年该位置的缩孔报废率为5%,经过一系列的探索,成功地将废品率降低为0.2%。本课题从铝合金压铸件缩孔的形成机理[1-5]和铸造条件两方面出发,分析铸件产生缩孔的原因,寻求改善措施,以期为日后解决铝合金压铸件缩孔问题提供参考。一、铝合金压铸件缩孔形成机理及形态--缩孔形成机理:导致铝合金压铸件缩孔的原因较多,追溯其本源,主要是铝合金从液相向固相转变过程中铝液补缩不足而导致。常见的缩孔原因有:①模温梯度不合理,导致铝液局部收缩不一致。②铝液浇注量偏少,导致料饼薄,增压阶段补压不足。③模具存在热结或尖锐区域。④模具的内浇口宽度不够,面积较小,导致铸件过早凝固,增压阶段压力传递受阻、铝液无法补缩。⑤铸造压力设置过低,补缩效果较差。图1为铝合金铸件缩孔形成的示意图。铸件缩孔形态:缩孔是一种铝合金压铸件乃至铸件常见的内部缺陷,常出现在产品壁厚较大、模具尖角和模温温差较大等区域。图2为某款发动机曲轴箱缩孔形态,缩孔呈似椭圆状,距离轴承油道孔约10 mm,内壁粗糙,无光泽。缩孔区域铸件壁厚较大,约为22 mm;油道孔销子前端无冷却水,模温较高。汽车发动机曲轴的两大轴颈(主轴颈和连杆轴颈)工作载荷较大,磨损严重,工作时必须进行压力润滑。在此情况下,轴颈的油道孔附近若存在缩孔,将会严重影响润滑效果。二、缩孔相关对策:铝合金压铸件产生铸造缺陷的原因有产品本身的结构特征、模具设计得浇注系统及冷却系统设计不合理、工艺参数设计不合理等原因[1~4]。根据常见的铸造缺陷原因以及铝合金铸件缺陷处理流程,探索解决铝合金压铸件厚大部位缩孔的相应对策。前期分析及对策:铸件缩孔的前期分析从容易操作的工艺参数出发,通过现场测量及观察,测得模具内浇口厚度为4 mm,计算的内浇口速度为40 m/s,产品壁厚*薄处为4.6 mm;料饼厚度为25 mm;铸造压力为60MPa。由经验可知,模具设计符合产品的结构特征,模具浇注系统应该不存在增压阶段补缩不足的问题。但是,增压阶段的铝液补缩与料饼厚度和增压压力有直接的关系,合适的料饼厚度与铸造压力才能形成内部组 织致密的铸件,因此,可以怀疑缩孔是由铸造压力偏低和料饼偏薄而导致的。前期消除铸件缩孔的对策分为两个:①铸造压力由之前的65MPa提高至90MPa;②料饼厚度有原来的25 mm调整为30 mm。采用上述措施后,经过小批量专流验证,缩孔率由5%减低为4.8%,效果不明显,说明工艺参数不是引起铸件缩孔的主因。中期分析及对策:由于引起铸件缩孔的本质原因是铝液凝固时补缩不足而导致,而模具温度分布不均容易导致铝液凝固顺序不合理,从而补缩不足,因此,中期对策分析主要从确保合理的模具温度入手。由产品3D模型可知,铸件缩孔处壁厚为22.6mm,壁厚较大,容易引起较高的模具温度。铝液凝固时,壁厚较大铸件内部铝液由于温度较高,尚处于液相或者固液混合相,而此时内浇口进行补缩的通道可能已经凝固。这样,在增压阶段铸件无法进行铝液补缩,从而有形成缩孔的可能。为确保合适的模具温度,采用热成像仪测得脱模剂喷涂后模具*高温度为272℃(见图3),高于正常的模具喷涂后温度,其他区域模具温度及其分布整体正常。因此,需要降低缩孔处模温。另外,测得此处冷却水孔底部距离模具型腔表面距离较大为20 mm,因为较大的热传递距离会降低模具的冷却效果,所以需要对冷却水孔进行更改。为降低缩孔处模具温度,主要采取3个方法:①改善模具冷却系统。将缩孔附件的冷却水孔深度加深,由距模具表面20 mm变成12 mm,以此快速带走附近模具热量,降低模温;将所有模具冷却水管与水管统一编号,一一对应,防止模具保全时装错,影响冷却效果[5,6]。②降低浇注温度,由675℃变为645℃。③延长缩孔处模具喷涂时间,由2 s变成3 s。实施上述整改措施后,缩孔区域模具喷涂后温度大幅度降低,约为200℃,属于正常范围。缩孔率有4.8%降低到4%,说明此类措施对缩孔具有一定效果,但不能彻底解决此区域的缩孔问题。后期分析及对策:通过前面两次改善,基本保证压铸模具处于理论上的合理状态,即浇注系统设计合理、冷却系统布置合适,工艺参数设计*优。然而,铸件缩孔率仍有4%之多。铸件缩孔处壁厚为22.6 mm,远大于其他部位的壁厚,较大的壁厚可能引起铸件中心凝固时补缩不足,增压结束后此区域还没有完全凝固,继续收缩产生缩孔[7~10],模流分析见图4。因此,如何解决铸件缩孔处的补缩不足,也许才是问题的关键。一般来讲,铸件的补缩时通过料饼→浇道→内浇口→铸件这条路径进行的。由于铸件厚大部位后于内浇口凝固,切断了增压后期的补缩通道,因此无法补缩。
缩孔是铝合金压铸件常见的内部缺陷,常出现在产品壁厚较大或者易形成热点的位置。一般来讲,只要缩孔不影响产品的使用性能,都以合格的方式来判定。然而,对于一些重要部位,如汽车发动机汽缸体的冷却水道孔或润滑油道孔,出现缩孔是不允许判定合格的。
某企业的一款铝合金制发动机曲轴箱,采用布勒28000kN冷室压铸机铸造,材质为ADC12合金,成分见表1。铸件毛坯质量为6.3 kg,后工序进行X射线探伤时发现第二个曲轴轴承孔油道出现缩孔,离油道约8 mm,存在较大的漏油风险。据统计,2017年该位置的缩孔报废率为5%,经过一系列的探索,成功地将废品率降低为0.2%。本课题从铝合金压铸件缩孔的形成机理[1-5]和铸造条件两方面出发,分析铸件产生缩孔的原因,寻求改善措施,以期为日后解决铝合金压铸件缩孔问题提供参考。一、铝合金压铸件缩孔形成机理及形态--缩孔形成机理:导致铝合金压铸件缩孔的原因较多,追溯其本源,主要是铝合金从液相向固相转变过程中铝液补缩不足而导致。常见的缩孔原因有:①模温梯度不合理,导致铝液局部收缩不一致。②铝液浇注量偏少,导致料饼薄,增压阶段补压不足。③模具存在热结或尖锐区域。④模具的内浇口宽度不够,面积较小,导致铸件过早凝固,增压阶段压力传递受阻、铝液无法补缩。⑤铸造压力设置过低,补缩效果较差。图1为铝合金铸件缩孔形成的示意图。铸件缩孔形态:缩孔是一种铝合金压铸件乃至铸件常见的内部缺陷,常出现在产品壁厚较大、模具尖角和模温温差较大等区域。图2为某款发动机曲轴箱缩孔形态,缩孔呈似椭圆状,距离轴承油道孔约10 mm,内壁粗糙,无光泽。缩孔区域铸件壁厚较大,约为22 mm;油道孔销子前端无冷却水,模温较高。汽车发动机曲轴的两大轴颈(主轴颈和连杆轴颈)工作载荷较大,磨损严重,工作时必须进行压力润滑。在此情况下,轴颈的油道孔附近若存在缩孔,将会严重影响润滑效果。二、缩孔相关对策:铝合金压铸件产生铸造缺陷的原因有产品本身的结构特征、模具设计得浇注系统及冷却系统设计不合理、工艺参数设计不合理等原因[1~4]。根据常见的铸造缺陷原因以及铝合金铸件缺陷处理流程,探索解决铝合金压铸件厚大部位缩孔的相应对策。前期分析及对策:铸件缩孔的前期分析从容易操作的工艺参数出发,通过现场测量及观察,测得模具内浇口厚度为4 mm,计算的内浇口速度为40 m/s,产品壁厚*薄处为4.6 mm;料饼厚度为25 mm;铸造压力为60MPa。由经验可知,模具设计符合产品的结构特征,模具浇注系统应该不存在增压阶段补缩不足的问题。但是,增压阶段的铝液补缩与料饼厚度和增压压力有直接的关系,合适的料饼厚度与铸造压力才能形成内部组 织致密的铸件,因此,可以怀疑缩孔是由铸造压力偏低和料饼偏薄而导致的。前期消除铸件缩孔的对策分为两个:①铸造压力由之前的65MPa提高至90MPa;②料饼厚度有原来的25 mm调整为30 mm。采用上述措施后,经过小批量专流验证,缩孔率由5%减低为4.8%,效果不明显,说明工艺参数不是引起铸件缩孔的主因。中期分析及对策:由于引起铸件缩孔的本质原因是铝液凝固时补缩不足而导致,而模具温度分布不均容易导致铝液凝固顺序不合理,从而补缩不足,因此,中期对策分析主要从确保合理的模具温度入手。由产品3D模型可知,铸件缩孔处壁厚为22.6mm,壁厚较大,容易引起较高的模具温度。铝液凝固时,壁厚较大铸件内部铝液由于温度较高,尚处于液相或者固液混合相,而此时内浇口进行补缩的通道可能已经凝固。这样,在增压阶段铸件无法进行铝液补缩,从而有形成缩孔的可能。为确保合适的模具温度,采用热成像仪测得脱模剂喷涂后模具*高温度为272℃(见图3),高于正常的模具喷涂后温度,其他区域模具温度及其分布整体正常。因此,需要降低缩孔处模温。另外,测得此处冷却水孔底部距离模具型腔表面距离较大为20 mm,因为较大的热传递距离会降低模具的冷却效果,所以需要对冷却水孔进行更改。为降低缩孔处模具温度,主要采取3个方法:①改善模具冷却系统。将缩孔附件的冷却水孔深度加深,由距模具表面20 mm变成12 mm,以此快速带走附近模具热量,降低模温;将所有模具冷却水管与水管统一编号,一一对应,防止模具保全时装错,影响冷却效果[5,6]。②降低浇注温度,由675℃变为645℃。③延长缩孔处模具喷涂时间,由2 s变成3 s。实施上述整改措施后,缩孔区域模具喷涂后温度大幅度降低,约为200℃,属于正常范围。缩孔率有4.8%降低到4%,说明此类措施对缩孔具有一定效果,但不能彻底解决此区域的缩孔问题。后期分析及对策:通过前面两次改善,基本保证压铸模具处于理论上的合理状态,即浇注系统设计合理、冷却系统布置合适,工艺参数设计*优。然而,铸件缩孔率仍有4%之多。铸件缩孔处壁厚为22.6 mm,远大于其他部位的壁厚,较大的壁厚可能引起铸件中心凝固时补缩不足,增压结束后此区域还没有完全凝固,继续收缩产生缩孔[7~10],模流分析见图4。因此,如何解决铸件缩孔处的补缩不足,也许才是问题的关键。一般来讲,铸件的补缩时通过料饼→浇道→内浇口→铸件这条路径进行的。由于铸件厚大部位后于内浇口凝固,切断了增压后期的补缩通道,因此无法补缩。
恒永兴金属材料销售
有限公司【022-86869388】在湖北省孝感市本地专业从事铝合金型材【石油裂化管】一站式,低,快,效果好 ([城市群])可送货上门。